Will the Skylines of the Future Be Made of Wood?
Eco-friendly timber is enabling the rise of “ply-scrapers” around the world
by Boyd Farrow
October 17, 2024
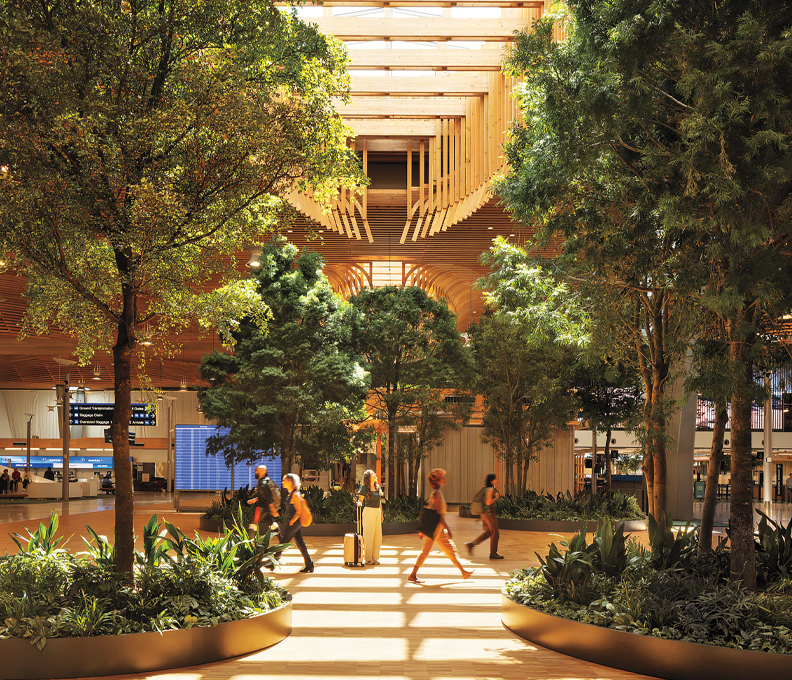
Portland International Airport, Oregon / Photo: Courtesy of Ema Peter
Anyone considering future-proof career options—a data scientist, perhaps, or an AI engineer—may want to add woodworker or even lumberjack to their list. This is not in case we all suddenly find ourselves, in some postapocalypse scenario, in need of log cabins to live in. Rather, it is because a growing number of architects, working with new high-tech engineered wood products as strong as steel and concrete, are already imagining tomorrow’s cities with towering timber skylines.
Plenty of statement buildings have already been constructed out of so-called mass timber—composites of compressed and bonded layers of wood—including Wyoming’s Jackson Hole Airport and Walmart’s new 350-acre campus headquarters in Bentonville, Arkansas. However, this material is increasingly being considered for a wide range of construction projects throughout the U.S.
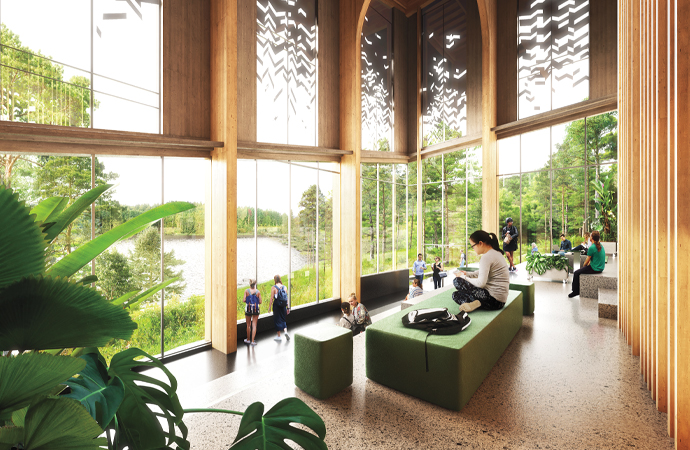
Lakehouse Wendelstrand, Mölnlycke, Sweden / Photo: Courtesy of ©SNØHETTA
Data from advocacy group WoodWorks shows that America had a total of 2,115 completed, in-design or in-construction mass timber buildings as of the end of March, compared with a paltry 50 a decade ago. This figure is now rising approximately 30 percent a year, as local building codes are rapidly being reviewed and state and federal funding continues to pour into innovations within the forestry sector.
The main driver for all this, of course, is climate change. Cement production accounts for eight percent of global carbon emissions, while steel is responsible for seven percent. The International Energy Agency claims that buildings account for 39 percent of the planet’s emissions: 11 percent from materials and construction and 28 percent from the energy needed to heat, cool and power them. Studies suggest that using mass timber—which stores carbon—for mid-rise structures could slash emissions associated with manufacturing, transporting and installing materials by almost a third.
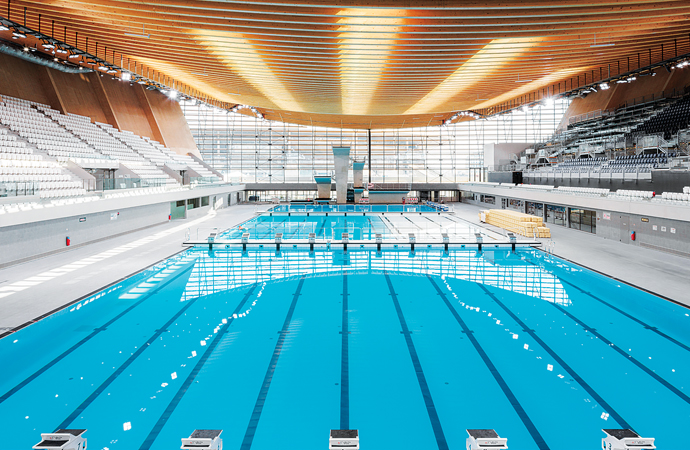
Aquatics Centre, Paris / Photo: Courtesy of @Architecture Venhoevencs & Ateliers 234/Salem Mostefaoui
Currently, the world’s tallest timber building is the 25-story Ascent in Milwaukee, an upscale residential structure that was completed in 2022. At 284 feet, it is almost the same height as New York’s iconic Flatiron Building. Architect Jason Korb, whose eponymous firm designed the 259-apartment tower—which features exposed timber columns, beams and ceilings—says the amount of carbon dioxide the building sequesters “is the equivalent of taking 2,400 cars off the road for a year.”
However, it is not only the planet that would benefit from a rise in mass timber construction, says Korb: “For many projects, wood would work out cheaper than cement and steel, and some states have so much fir or yellow pine lumber they don’t know what to do with it. Even worse, we’ve been getting these terrible wildfires because forests have been allowed to get out of control.”
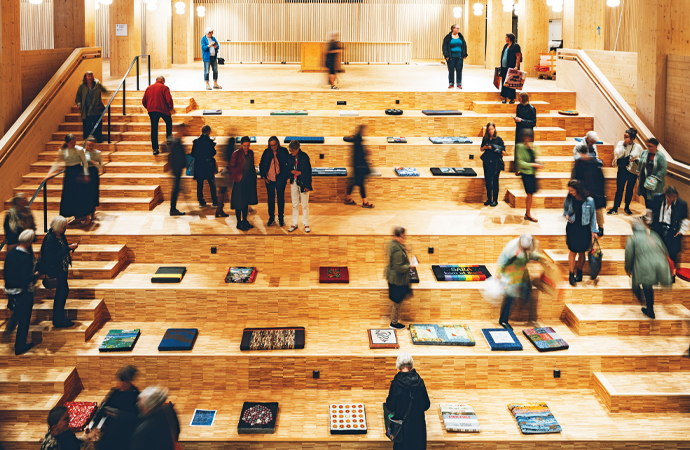
Sara Cultural Centre, Skellefteå, Sweden / Photo: Courtesy of Jonas Westling
U.S. forestland grew by some 18 million acres between 1990 and 2020, according to the UN Food and Agriculture Organization—an area equivalent to about 1,200 NFL football fields appearing every day. Less than two percent of this land is harvested each year. America’s largest architecture firm, Gensler—which designed Jackson Hole Airport, Walmart’s new HQ and Southstone Yards, the largest mass timber building in Texas—claims that enough wood to construct a 100,000-square-foot building is grown every seven minutes.
Advocates of engineered wood claim that there are even more economic advantages for developers. “As mass timber panels are precision-cut and prefabricated, construction schedules could be far shorter, with reduced waste and labor costs,” says Korb. “This means potential savings on nearly all bread-and-butter buildings up to around seven stories.” For some taller buildings, economies of scale coupled with the use of lighter materials could lead to further savings. “When Ascent reached a certain height,” says Korb, “it became cost-effective to add extra levels.”

Southstone Yards, Frisco, Texas / Photo: Courtesy of Ryan Conway/Gensler
Katie Mesia, a principal at Gensler and the firm’s sustainability director, points out that while wholly wooden mega-skyscrapers are probably not a good idea, additional stories made from mass timber could easily be assembled—like “livable jigsaws”—on top of many existing buildings. Furthermore, these prefabricated panels could easily be “dismantled and recycled,” she says. Ascent’s success in meeting multiple safety tests on its path to approval—previously, America’s tallest timber tower was an eight-story, 95-foot-high condo in Portland, Oregon—has led to cities throughout the country exploring mass timber options and revising local building codes.
New York, for one, has launched a program to raise awareness of the benefits of using the material and identify development opportunities throughout the city. Korb has won approval for a mixed-use project in St. Louis and has a project in the pipeline in Texas.
Meanwhile, work has begun in Milwaukee on an even taller timber tower. The 32-story Edison, which will have 383 apartments plus retail space, has been designed by global engineering firm Thornton Tomasetti and Chicago architects HPA. Reportedly, Thornton Tomasetti is also developing a mass timber project for New York City that would be 30 stories tall.
Of course, the proliferation of such wooden towers will depend on the public’s confidence in the materials, construction techniques and testing procedures. In the final evaluation on Ascent’s lengthy path to approval, the U.S. Forest Service tested glulam (glued laminated timber) columns that were shipped from Austria to its national research lab in Wisconsin. After finding the columns were difficult to burn, the Forest Service awarded them an exemplary three-hour fire-resistance rating because they maintained their structural integrity.
“In any blaze, wooden beams would slowly char rather than combust, and even then, the timber would burn slowly and steadily, unlike steel, which warps and suddenly collapses,” says Korb. “Hopefully, safety concerns over timber buildings will disappear as they become more common.”
Ironically, Mesia notes that timber structures can improve the health of their inhabitants as well as the planet. “Studies show that they can help lower heart rates, blood pressure and stress levels,” she says. “Aesthetic qualities aside, in every culture wood makes people feel happier and calmer.”
The Walmart campus—which, with more than 2.4 million square feet of office space, is the largest mass timber project in the U.S.—is vital to the retail giant’s Big Nature master plan, designed to “reinforce sustainable living and holistic well-being” amid a mosaic of landscapes varying from woodland to wetlands. Other companies are also turning to wooden structures either to underscore their integrity or advertise their green credentials. Sportswear maker Under Armour says its “raw” mass timber building in Baltimore highlights the company’s authenticity, while also demonstrating how the company “walks the walk on its sustainability commitments.”
“A lot of corporations have made very serious climate commitments, which is, after all, how they have won over many of their customers,” says Mesia. “Investing in sustainable architecture that stands out is a way of reinforcing those commitments—and their public image.”
Mesia believes that for every high-profile mass timber project that has been announced, a logjam of others is still under wraps, as developers keep a close eye on public opinion and potential changes to building regulations. “We’re definitely seeing a trend in large corporate campuses starting to embrace wood. But often when a company is spending a lot of money on something radical, it doesn’t want to be the first,” she says. “It wants to be the first to be second.” Ultimately, many architects and building engineers believe a surge in mass timber construction throughout the U.S. is inevitable, given the current administration’s commitment to meeting environmental targets, growing the economy and creating thousands of new highly skilled jobs.
Sustainable forest management involves a great deal more than planting saplings to replace felled trees. In Europe, where the industry has long been far more vertically integrated, it is becoming increasingly high-tech. Nurseries grow seedlings under optimal conditions—protected by fungicides, then chilled in refrigerators and disoriented by dim light to make them more robust. Trees are continually monitored via satellites and drones and gathered by data-mining “smart harvesters.”
Eventually, an array of engineered wood products—curved beams, chunky columns, slats and many other construction components—is laser-cut using CNC (computer numerical control) machines that look like they belong in aircraft assembly plants rather than sawmills. All the wooden panels for the Ascent building were shipped from Austria. The timber for The Edison, its soon-to-be-loftier neighbor, came from Finland. Yet Korb is optimistic that America’s environmental imperative will lead to more homegrown operations seamlessly supplying products of comparable quality and consistency.
In March, one of the U.S.’ largest mass timber manufacturers, Timberlab, announced plans to open a state-of-the-art 250,000-square-foot facility in Oregon—the heart of the American lumber industry—to supercharge adoption of engineered wood products. This followed the Biden Administration’s pledge last year to establish a Mass Timber Tech Hub in Oregon and Washington as part of its effort to “use advanced material science to develop low-carbon housing solutions.”
“Some European countries have more experience of wood technology, so there is a lot of know-how in the value chain. In some areas, we’re playing catch-up,” says Korb. “Still, for those of us who can see the benefits of mass timber, things are starting to look up.”